Separation Of Ethanol And Water By Rotary Evaporator
Vacuum Distillation Rotary Evaporator is mainly used for continuous distillation of large quantities of volatile solvents under reduced pressure. In particular, the concentration of the extract and the distillation of the receiving liquid during chromatographic separation can separate and purify the reaction product. The basic principle of Vacuum Distillation Rotary Evaporator is vacuum distillation, that is, under reduced pressure, when the solvent is distilled, the distillation flask is continuously rotating. Vacuum Distillation Rotary Evaporator structure: The distillation flask can be a pear-shaped or round-bottomed flask with a standard grinding mouth interface, connected to a vacuum pump through a high reflux serpentine condenser, and the other opening of the reflux condenser is connected to a ground-mouthed condenser. A receiving flask is connected for receiving the evaporated organic solvent. There is a three-way piston between the condenser tube and the decompression pump. When the system is connected to the atmosphere, the distillation flask and the liquid-contacting flask can be removed to transfer the solvent. When the system is communicated with the decompression pump, the system should be in a reduced state. pressure state. When in use, the pressure should be reduced first, and then the motor should be started to rotate the distillation flask. At the end, it should be stopped first and then vented to the atmosphere to prevent the distillation flask from falling off during rotation. As a heat source for distillation, it is often equipped with a corresponding constant temperature water tank.
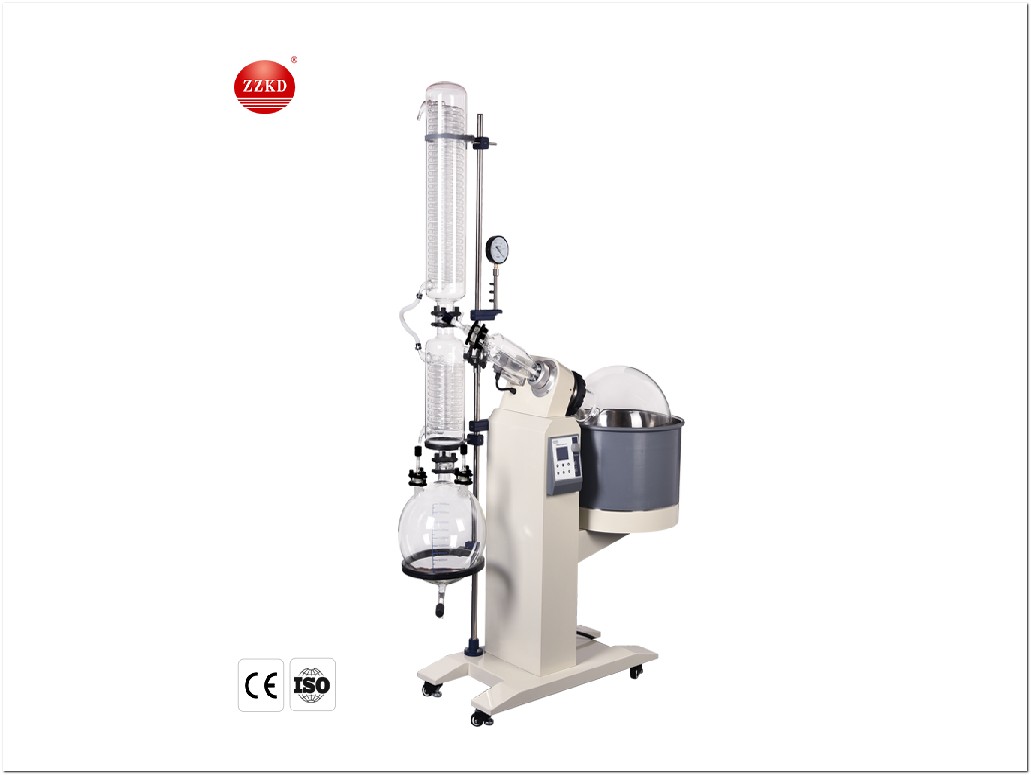
Use a Rotary Evaporator to separate ethanol and water as follows:
1. Use a Rotary Evaporator for analysis of components in waste solvent DMF
It can be known from the synthetic reaction equation of TATB that the waste liquid mainly includes DMF, water (brought in by ammonia water), and ethanol (by-product). Due to the reheating during the reaction, the decomposition of DMF may generate a small amount of formic acid. The waste solvent DMF may contain a small amount of TATB particles and a small amount of unreacted intermediates. The collected DMF waste solvent is left to settle and filter, and the particulate matter is filtered out, and the collected mother liquor is analyzed for relevant components.
1.1 Analysis of solvent components in waste solvents
The contents of DMF and ethanol in the waste liquid were detected by gas chromatography, and the moisture content in the waste liquid was obtained by Karl Fischer analysis.
1.2 Separation of ethanol and water under reduced pressure by rotary evaporation
Due to the large difference between the boiling points of ethanol, water and DMF in the waste liquid, in the experiment, ethanol, formic acid and water will directly enter the vacuum pump before being condensed by high vacuum distillation. Therefore, the recovery process in the experiment is divided into three stages, and each stage obtains Substances with different main components are easy to classify and handle. The first stage: heated to 75~78℃ under normal pressure, the main distillation is the azeotrope of ethanol, formic acid and water, which is directly incinerated in the experiment. In the industrial production process, the ethanol mixture can be used as fuel and other other use. The second stage: under reduced pressure (0.08MPa)
When heated to 60~70℃, the main distillation is water and a small amount of DMF, which is treated with lye. Under the action of alkali, DMF is decomposed into formate and dimethylamine, DMA is driven out with air, and incinerated with oxygen-enriched air to convert it into N2 and CO2, formate can be directly treated by biological method. In the third stage, using a high vacuum chemical pump, decompression (0.29~9mbar) and heating to 29~54°C, the main distillation is DMF solvent. During the recycling process, we carried out a detailed study on the degree of vacuum, temperature, purity of the recovered DMF, and recycling.
2. DMF recovery and detection
2.1 The relationship between vacuum degree and temperature in vacuum distillation of waste solvent DMF
Through several sets of experiments to study the temperature of DMF under vacuum distillation under different vacuum conditions, the relationship between vacuum degree and temperature in the vacuum distillation process was mastered, which provided data for the determination of waste solvent DMF recovery process. In this experiment, the relationship between temperature and vacuum degree during the decompression process was measured. When the vacuum degree is controlled at 9 mbar, the distillation temperature of DMF can reach 54 °C, but the distillation speed is found to be relatively slow in the experiment; when the vacuum degree reaches 0.29 mbar, the distillation temperature of DMF is as low as 29 °C, and the distillation speed is fast, it can be clearly seen that , as the vacuum degree increases, the distillation temperature of DMF decreases. Within a certain vacuum range of 0.29~1.6mbar, through multiple sets of parallel experiments, the purity of the recovered DMF is 92%~97.8%, although there is a certain gap between the purity of the recovered sample and the purity of analytical pure DMF, the main difference It is reflected in the moisture. The recovered DMF is mainly used in the TATB synthesis reaction. The chlorine-free synthesis reaction of TATB mainly uses ammonia water as an aminating agent. A group of DMF reagents with lower purity was planned to be used as the amination test to investigate whether it would have a certain influence on the synthesis of TATB.
To learn more about rotary evaporators:
R-1050 rotary evaporator,
RE-1002 rotary evaporator, etc., please feel free to contact us!